SPLINTERS
Tennessee Valley Woodworkers
Vol. 21/ Issue 1
January 2006
Editor: Chuck Taylor
Meeting Notice:
The next meeting of the TN Valley Woodworkers
Will be held, January 17th at 7:00 p.m. in the
Duck River Electric Building, Decherd, TN
All interested woodworkers are invited!
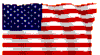
Please remember, in your thoughts and prayers,
all our Troops around the world and those on the way home.
The following people have agreed to serve as contacts for their particular
skills. If you have questions, suggestions for activities, or other
comments relating to these skills, please call these folks. Their
interest is to help the club better serve their area of expertise.
Your participation with them will help them achieve that goal.
Design: Tom
Cowan 967-4835
Finishing: Phil
Bishop 967-4626
Turning: Tom
Church 967-4460
Carving: Harry
May 962-0215
Sharpening: Bob
Reese 728-7974
Joinery: Ross
Roepke 455-9140
Maurice Ryan 962-1555
Health and Safety
List of Club Officers
President:
Loyd Ackerman
V. President: Tom
Cowan
Secretary: Bob
Lowrance
Treasurer: Henry
Davis
Publicity: Larry
Bowers
Newsletter Editor: Chuck Taylor
Web-Master: Richard Gulley
MEMBER INFORMATION
Club Dues
Club Dues are payable in January.
Our Dues are $10.00 for a single membership, and $15.00 for a family membership.
If you can't attend a meeting soon you can mail your dues check to
Henry Davis, 247 Delight Lane, Tullahoma, TN 37388.
MEMBER INFORMATION CHANGES
We strive to always keep the club
membership roster up to date. If you have changes to your home address,
phone number or email address please let us know so we can update our membership
list. Contact Henry Davis at 931-393-3191 or hdavis@cafes.net
WELCOME TO OUR NEW MEMBERS
Wayne Beam, Tullahoma
David and Yolanda Lacy, Winchester
THANKS
Thanks to Tom Gillard for his diligent efforts in publishing
the TVW Newsletter for the past eight years. He has done an outstanding
job and a great service to the club and members.
A special thanks to all the people who worked on the 20-year
Anniversary Celebration Dinner, making it a tremendous success for club
members and guests. The grand door prizes ($150 Woodcraft certificates)
were won by Ross Roepke and Dan Maher.
SHOW AND TELL:
Loyd Ackerman showed a video presentation of a Grandfather clock made for
his mother-in-law. The video showed various views and stages of completion
during the making of the clock case.
Tom Gillard brought two Sailboats,
one mounted to a natural edge base.
Ken Gould brought and discussed some very old detail trim planes
used
by his father.
Henry Davis showed a spalted maple bowl,
finished with sanding sealer and minwax.
Ross Roepke showed and discussed a solid mahogany table
with
curved legs. The drawer slides were made of poplar and the drawers had
“secret
compartments” hidden in the back. Ross discussed the difficulties encountered
in some of the manufacturing techniques. He also brought samples of crosses
he made for a church fundraiser.
Jim Acord brought and discussed a brochure from U-Bild, a supplier
of woodworking plans. Their web site is u-bild.com. He also brought and
distributed a booklet, “The Tree Book”.
Dick Wollam displayed a basswood carving
of flowers, a walking stick with very detailed
carvings and an owl carved from
western cedar.
Jack Rowe showed a small cherry table,
finished with Danish oil and coats of polyurethane on the top surface.
Mary Ellen Lindsay displayed her carving of a cup,
made of walnut.
Fred Heltsley brought and discussed a small
pipe rack with clay pipes.
Bob Lowrance brought a “Santa”
carving he had carved while attending the John C. Campbell School.
Billy May brought a basswood bull
he carved for a friend.
Bob Leonard showed items he had
made over the years. They included a knife, carvings of a dog, ax &
stump and cowboy boots. He also discussed two books for beginning carvers.
Wayne Beam brought two pedestal stands.
One was the first one he built and the other was the last one he finished.
Jim Van Cleave discussed his experience in cutting wax candles on his
bandsaw. The job left a major buildup of wax on the blade and the saw would
not run. He also discussed the accident he had during the cleaning of the
blade and the guide bearings (cut his finger).
Basswood
Among the most
important of America's nectar-producing trees, the basswood makes itself
at home along city streets as well as in the forest. In cityscapes, nurserymen
call the hardy, decorative tree American linden. But in the woods, it's
basswood, beetree, lime, or whitewood. Regardless of its name, basswood
has proven its value. Indians of New York state's Iroquois nation carved
ceremonial masks from the sapwood of living basswood trees, then split
the green-wood masks from the trunk. The gummy inner bark provided bandages.
And from its dried fibers they wove rope.
Beekeepers even today appreciate the quality of basswood-derived honey.
In summer, the tree's fragrant flower clusters provide a strong-flavored
nectar. Basswood stock also becomes the very boxes in which the honeycombs
are stored and shipped.
Carvers prefer basswood because it holds detail well, doesn't split,
has straight-grain, and carves easily. They usually prefer air-dried, slow-grown
northern stock. Basswood also can become drawer stock, hidden furniture
parts, and painted items. In industry, it plays a role as boxes and food
containers. As veneer, it can underlie fine cabinet woods in plywood. This
light, versatile wood also works for picture frames, toys, and millwork
such as window sashes. It even makes fine turning wood.
It would be hard to find a wood more perfect for carving. A sharp knife
or gouge slides through it as if cutting butter. And the finish of a clean
cut looks lustrous.
· Because basswood takes fine detail, it's great
for relief, figure, and chip carving.
· Basswood requires control or your carving tool may go further
along a stroke than planned.
Additional information about basswood:
· Basswood's low-hardness rating makes it ideal for hand tools.
· Power planing basswood poses no problems. You'll find jointing
effortless, too.
· Because the wood is dense, ripping requires a rip-set blade
with 24 teeth or less to avoid burning. In crosscutting, it won't tear
out or chip.
· Use sharp bits and don't rush the router when shaping basswood,
as its tight grain and density does tend to burn (although burns easily
sand off).
· Unlike some other lightweight, straight-grained woods (such
as redwood), basswood fastens well with nails or screws. And it's not necessary
to predrill.
Sanding basswood proves to be a soothing, smoothing task. But when
it comes to staining, blotching can result. If uneven staining appears
on a test piece, apply wood conditioner before staining. Remember, though,
even wood conditioner won't subdue discolored streaks in the wood.
Wood-Online
Shop Tip of the Day

A piece of pipe makes button sanding a cinch.
Wooden buttons often need to be sanded before use. But it's sure tempting
to stick them into place without sanding because they're so hard to hang
on to. Push the stem of the button into the end of a piece of copper or
plastic pipe about 12" long to give yourself a better grip. Try different
sizes of pipe and tubing for various buttons.
--From the WOOD magazine shop
Web Sites of interest.
Wood Central
See you on the 17th.
click on the image to go to these sites
Special contributors to Club functions